Fundamental principles in combustion engines are investigated experimentally and computationally. Detailed computational modeling
of processes inside combustion engines involves modeling of thermodynamics, combustion and emission formation, fluid flow, heat transfer and the interactions of the phenomena.
This work is mainly undertaken in our collaboration with MAN Diesel & Turbo A/S, which started up in 2006. As a part of this, some essential main topics are investigated:
Scavenging and Swirling Flow in 2-Stroke Diesel Engines
The goal is to provide new knowledge and simulation capabilities on scavenging and swirling flows. We are focusing on a flow type that until know only has received modest interest: confined swirling flow without the classical vortex brake down. The detailed goals are:
-
To apply new optical measurement techniques to provide a completely new level of detail in our observation: quantifying the dynamics of flow structures
-
To apply and improve newly established mathematical models using the experimental data
-
To clarify the effect of imperfections and asymmetries of boundary conditions
-
To measure concentrations and scavenging efficiency in transient experiments involving density difference and valve motion
-
To establish how reliable numerical simulations can be performed – partly by improving existing models for turbulence
-
To demonstrate the results by measurements on a real engine
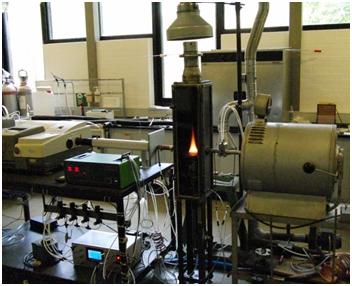
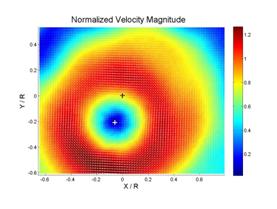
Figure 1: Optical measurements of swirling flow in experimental cylinder and a CFD simulation of local velocities
Heat transfer in two stroke diesel engines for large ship propulsion
As a part of the activities a project focuses on estimating the heat transfer to the piston surface at flame impingement during combustion. The work is numerical using CFD (the STAR-CD code). Simulations of an impinging hot air jet on a flat plate are carried out as a simplified case to imitate the flame impingement on the piston surface. The simulations are used to investigate the heat transfer associated with this flame/wall interaction.
Measurement of dynamic heat transfer is another important activity. Temperatures and heat flux in and around the engine cylinder of a large 2-stroke diesel engine is measured dynamically with specially designed high speed thermocouples. The thermocouples have such a fast response that resolution of the surface temperature can be obtained down to one tenth of a crank angle degree.
Numerical calculations of heat conduction and convection is carried out and compared with the results from the experiments.
Radiation in 2-stroke diesel engines
The aim of the project is to enhance capabilities of current Computational Fluid Dynamic (CFD) models. This will increase the possibility for improved prediction of the complex physical phenomena occurring in marine diesel engines and in particular contribute to a more accurate computational prediction of local processes that are directly responsible for formation of harmful emissions. The results and the developed numerical methodologies may eventually lead to improved design tools that will become important in view of future emission regulations for marine propulsion. Detailed computational modeling of processes inside combustion engines involves modeling of combustion, fluid flow and heat transfer phenomena and their mutual interactions. Currently, influence of heat radiation from gasses and particles is usually not or at least only in very simplified ways accounted for in state-of-the-art models of in-cylinder flow in combustion engines. This project focuses on improvement of the radiant heat transfer models. The approach will be to adopt large, detailed and computationally demanding modeling of radiation phenomena developed by physicists for engineering purposes. Since computational resources are limited a compromise must be found between fidelity of the employed model and computation times that are under reasonable limits within an engineering framework. This will be done by systematic sensitivity analysis of model simplifications and thorough validation against experimental results. Those studies are necessary to determine how the computational power is best spent and where the modeling approach is lacking. Different laboratory flames with increasing complexity levels will be used for validation purposes. This incremental approach is essential to identify where the radiation model becomes deficient. The most complex laboratory flame should comprise the features of a true diesel engine flame as much as possible. However, it must have a simple geometry and be stationary to enable accurate measurements and fast CFD computations. Ultimately the model will be validated against measurements performed in the MAN Diesel & Turbo test engine with optical access.
Project partners: MAN Diesel & Turbo A/S, Norwegian University of Science and Technology, Dep. of Energy and Process Engineering (NTNU), Combustion Research Facility at Sandia National Laboratories in California (SANDIA), The Optical Diagnostic Group at RISØ DTU, Politecnico di Milano (POLIMI).
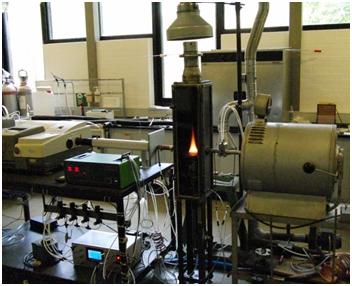
Figure 2: FTIR measurements of radiation from a premixed flame