The future energy supply for transportation, which to a large extend include combustion engines, will have to be based on other fuels than conventional crude oil based fuels. It is therefore of outmost relevance to include alternative fuels in our research and teaching program.
Ammonia/Hydrogen
The activities about applying ammonia/hydrogen as a fuel for SI engines started up as DTU announced the invention of the ammonia pill which, together with a catalytic converter, could serve as a compact H2 storage for fuel cell cars. Our intention was to investigate the ammonia pills potential as energy storage for combustion engines. It was believed that only partially converted NH3 would serve as an excellent and carbon free fuel for SI engines. This has indeed shown to be true. Previous concerns about high fuel NOx from the ammonia engine has also shown to be unjustified. Preliminary investigations actually show lower NOx emissions from NH3/H2 compared with gasoline on the same engine. The engine emits unburned NH3 which may be used to reduce NOx significantly by selective catalytic reduction (SCR) over a catalyst in the exhaust system.[Moerch, C.S. et. al., 2011].

Figure 1: Ammonia/hydrogen test engine.
DME
ICEG has been involved with DME application for combustion engines since the beginning of the area of this fuel in the middle of the 1990’s. DME is an attractive alternative to diesel due to a high cetane number, low toxicity, high well to wheel efficiency even from renewable sources, but first of all due to its very low soot propensity.
The homogeneous charge compression ignition engine (HCCI) is an engine concept with very low NOx emissions. The reason for that is a combination of very fast combustion at low temperatures. The HCCI research in our group has mainly concerned the use of DME as a HCCI fuel. Methanol addition to the fuel as well as exhaust gas recirculation has been used to control the ignition timing and different combustion chamber geometries have been used to minimize knocking and noise. [Pedersen, T.S. and Schramm, J., 2007] [Pedersen, T.S. et. al., 2010] [Pedersen, T.S. and Schramm, J., 2010].
Project partner: National Traffic Safety & Environmental Laboratory, Japan.
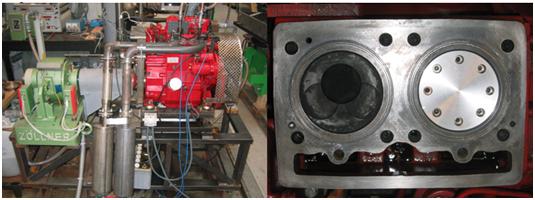

Figure 2: A HCCI 2-cyliner test engine is shown on the picture to the left. The right cylinder is running HCCI on DME, the left one is a normal diesel opearting cylinder. The picture to the right shows Mr. Sato from NTSEL and Mr. Hansen from ICEG in front of a Japanese DME truck.
DME is also studied as a fuel for small two stroke diesel engines. ICEG has developed a small engine of this type for application in small very fuel economic cars, the so-called “Ecocars”. The first generation engine was a 50cc piston ported crankcase scavenged two-stroke engine. It employed direct injection of DME through a GDI type electronic injector at 100 bars. Fuel line pressure was maintained by pressurization of the fuel tank with helium. [Hansen, K.R. et. al. 2009]
Later on a new engine was built based on crankshaft, conrod, piston and an air-cooled cylinder from a 50cc Peugeot two-stroke SI scooter engine. [Hansen, K.R. et. al. 2011].

Figure 3: The ICEG developed 50 cc 2-stroke DME CI engine
Another project focuses on DME from biomass. The technological challenges related to the efficient use of bio-fuels in conventional engines are the focus this project, where experimental and simulation work will advance our knowledge on specific frontiers related high performing bio-based transport fuels. One of the main goals are to deepen our understanding of the relative merits of these fuels’ value chains, between which we could expect that the actual competition will take place as the market gets more mature.
This project intends to systematically investigate the performance of second-generation bio-fuels. A test facility is developed for parallel studies of different bio-fuels in various state-of-the-art engines provided by the industrial partners. This enables a direct comparative study of the obtained results.
Furthermore, theoretical investigation will be carried out to deepen the fundamental understanding of the thermo-chemical processes involved. This involves adaption of simulation tools for prediction of combustion and emission formation, to support further technological development.
Project partners: Dept. of Energy and Process Technology, NTNU, Norway. Volvo Powertrain/ Volvo Technology, Sweden. SAAB Automobile Powertrain AB, Sweden. LOGE AB, Sweden. CHEMREC AB, Sweden. Ford Forschungszentrum Aachen, Germany.
Ethanol

Figure 4: International Energy Agency Banner.
Ethanol is an obvious candidate for fuelling SI engines in a more sustainable future. It can be and is already being produced from biomass. Being liquid makes it an obvious choice for the existing infrastructure on the fuel market. ICEG is representing Denmark in the International Energy Agency, Agreement for Advanced Motor Fuels (IEA AMF). As a part of this Associate Professor Jesper Schramm is responsible for the ethanol annex of IEA AMF. In this context ICEG has produced an international review report on the application of ethanol as a fuel for road transportation [Larsen, U. et. al., 2009]. As a part of this ethanol’s miscibility with water and gasoline has been investigated. This is particularly relevant in a situation where it is possible to fuel your vehicle with both gasoline and hydrous ethanol – like in Brazil [Johansen and Schramm, 2010].

Figure 5: Phase diagram for ethanol-water-gasoline.
An ethanol engine is under development in the department. The application is connected to our “Ecocar” activities.
Rape seed oil
Cold pressed rapeseed oil (KRO) has been investigated as a fuel for light duty vehicles. The project has been coordinated with another project in which the use of KRO for heavy duty vehicles has been investigated.
KRO has some environmental advantages compared to biodiesel. The yield of liquid fuel in relation to area of land used for growing is more than 20% higher, and the energy consumption for the fuel production and distribution is less. Furthermore, the capital required for building the production facilities is less and the filter cake left from the production can be used as feed for livestock.
However, there are some disadvantages when the fuel is applied to a diesel vehicle. First of all KRO has to be heated to 75-90ºC in order to have the proper flow characteristics. This means the vehicle must start up on ordinary diesel fuel and the engine has to run on diesel for some time in order to clean up the fuel system for KRO before turning off the engine. Therefore the fuel system of the vehicle must be reconstructed in order to be able to handle two different fuels. This implies a separate tank for KRO and a heating system where the exhaust heats up the KRO fuel system to the appropriate temperature.
Generally, the application of KRO in the vehicles was followed by many problems in practice. However, it is not unlikely that these problems could have been avoided if more carefulness, especially with the lubrication change intervals, had been practiced by the car owners. On this background it is recommended that KRO application in the future is applied by large carfleet owners, where careful observation of the vehicles is possible.
The emission measurements generally showed increased emissions of particulate matter with KRO compared to ordinary diesel. The number of particulates where also higher with KRO, and particularly the emissions of polyaromatic hydrocarbons (PAH) were higher with KRO. The emissions of CO, HC and CO2 seemed to be a little higher with KRO compared to diesel and the NOx emissions seemed to be a little lower.
The emission measurements indicated that the vehicles were not able to adjust completely from diesel to the new fuel. The combustion process was not as complete as with diesel. [Nielsen, C.S. et. al., 2010] [Ivarsson, A. et. al., 2010] [Nielsen, C.S., et. al., 2011]
Project partners: The Danish Traffic Authority, Technological Institute, Denmark.

Figure 6: Light-duty truck tested on rape seed oil
Low Sulfur Marine Fuels
Future fuels for marine purposes will be regulated with respect to sulfur content. Inside the engine the sulfur is converted to sulfuric acid which causes corrosion in the engine. The sulfuric acid is normally neutralized by basic compounds in the lubricant. However, if the fuel contains less sulfur this could result in other problems like scuffing if the lubricant is not adjusted to the lower content. ICEG work on developing and experimental verifying models that describes the interaction between fuel sulfur content and the contact between sulfuric acid and the cylinder liner surface inside the engine.
Project partners: MAN Diesel & Turbo A/S.